Northspyre Blog
Expert insights & resources
Stay informed with the latest tech trends, industry insights, and best practices for real estate development.
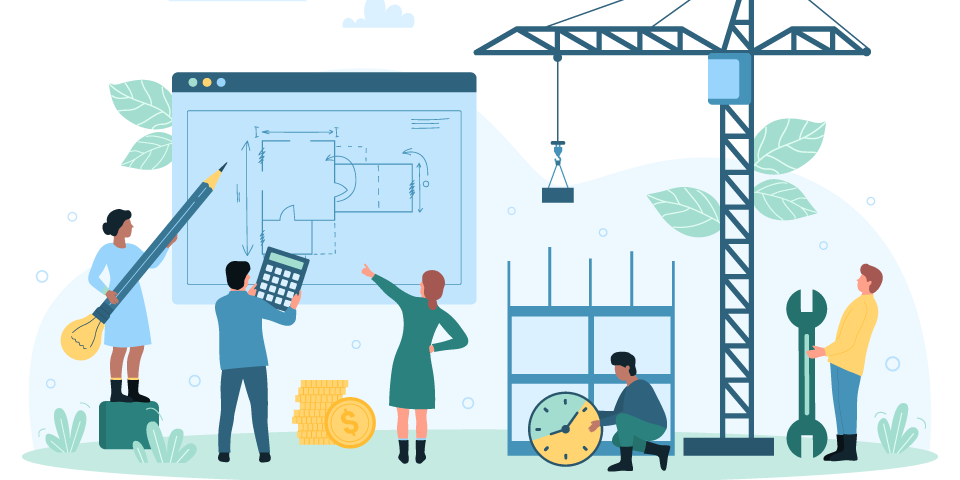
Market Trends, Real Estate Development
7 Trends Shaping the Future of Retail Real Estate
Adapting to meet challenges and unlock new potential.
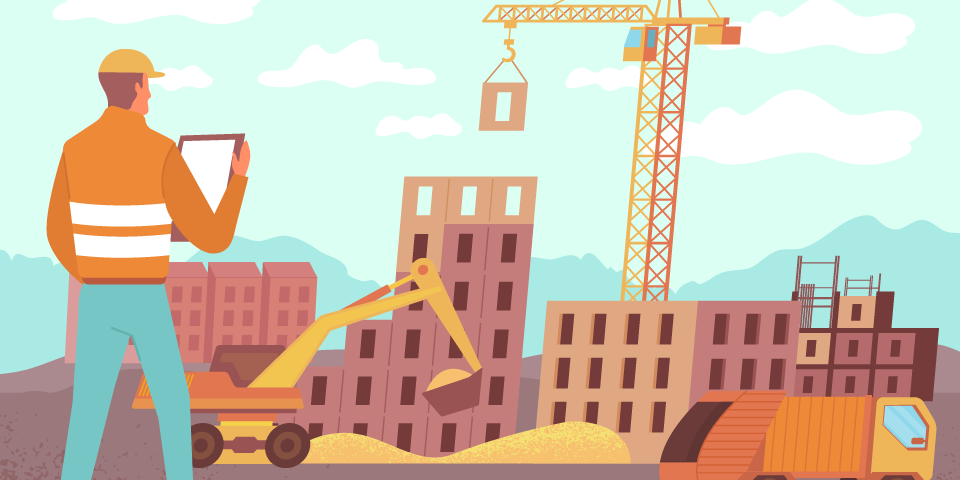
Market Trends, Real Estate Development
Understanding the Turbulence: the CRE Outlook Beyond 1Q25
Discover key CRE market insights for 1Q25 and beyond.
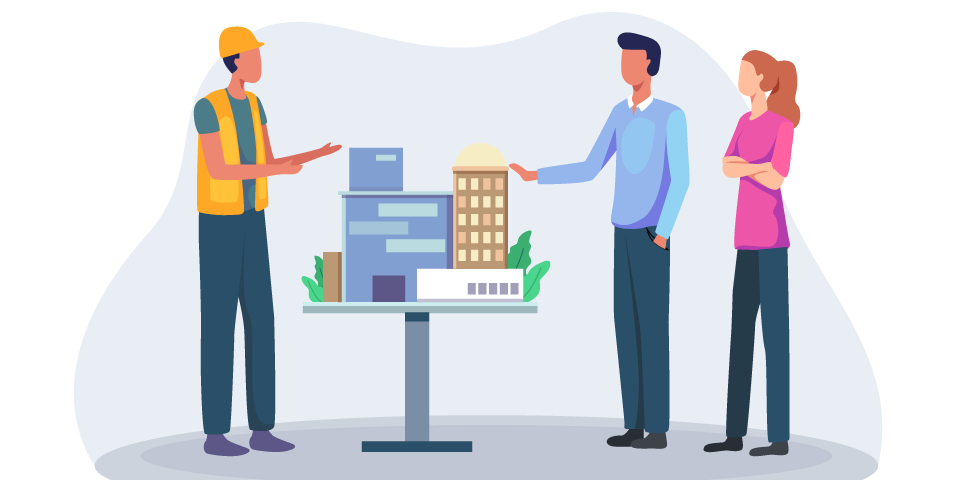
Market Trends, Real Estate Development
Unpacking the Impact of Tariffs on Commercial Real Estate Development
Learn how tariffs will impact CRE development in the short and long term.
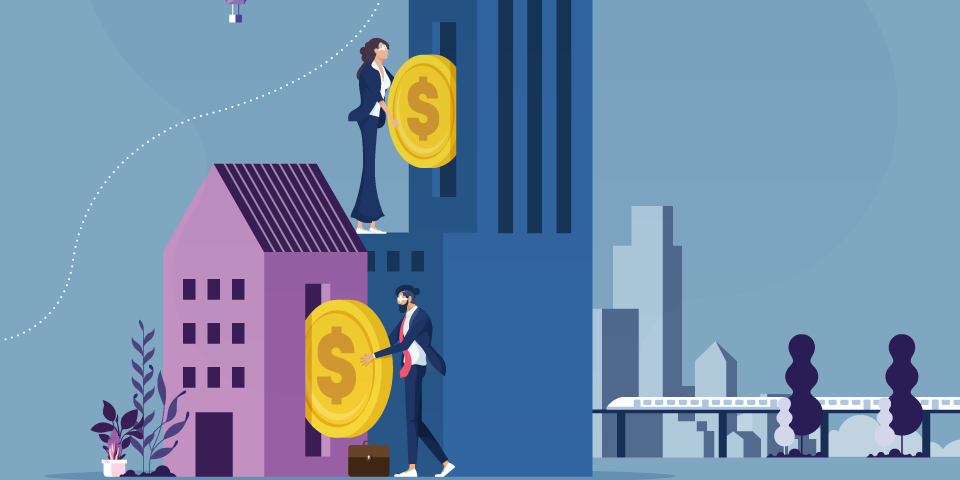
Project Management, Real Estate Development
Mezzanine Financing: A Real Estate Developer’s Guide
Learn the ins and outs of leveraging mezzanine financing for real estate developers.
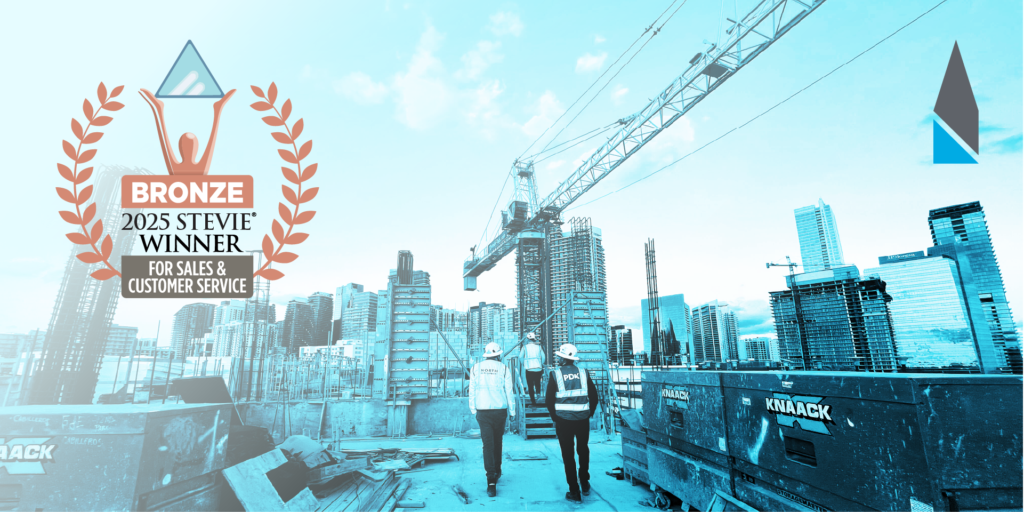
Real Estate Development, Technology
Northspyre Wins 2025 Stevie Award for Achievement in Customer Experience
Northspyre receives Bronze Stevie Award for Achievement in Customer Experience.
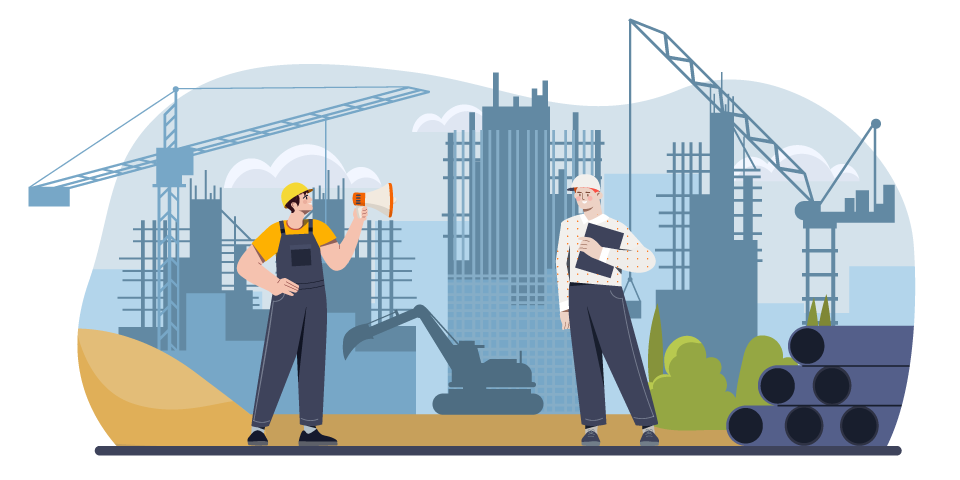
Project Management, Real Estate Development
CRE Developer’s Guide to Securing Government Approvals
Here's everything developers deep to know about the government approvals landscape.
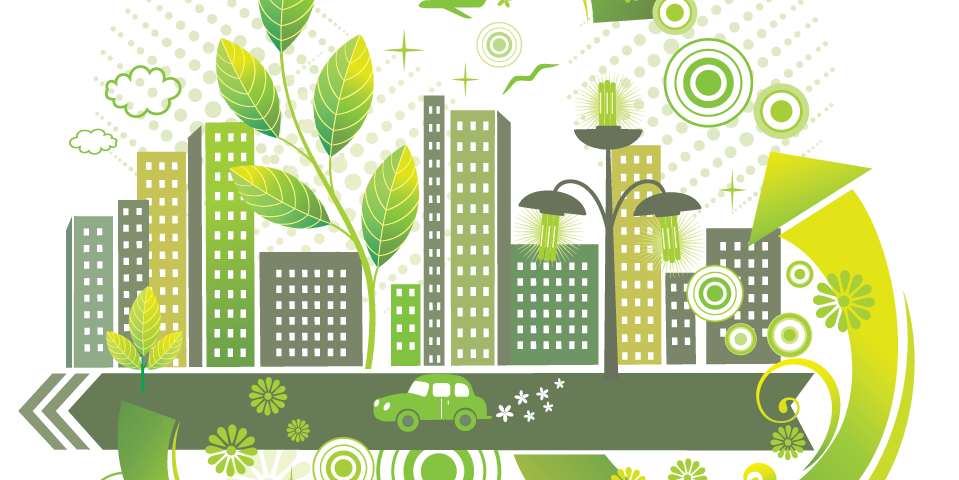
Market Trends, Real Estate Development
How Green Energy Leases Bridge the Sustainability Gap in Multifamily
Green energy leases are helping developers meet sustainability requirements on multifamily properties.
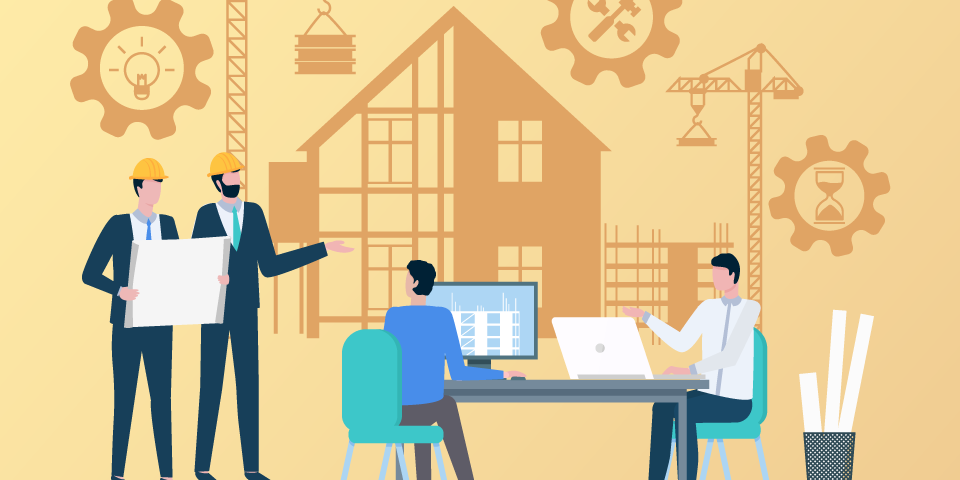
Market Trends, Real Estate Development
Office-to-Residential Conversions: Why Demand Is Soaring
Explore key drivers, challenges, and case studies.
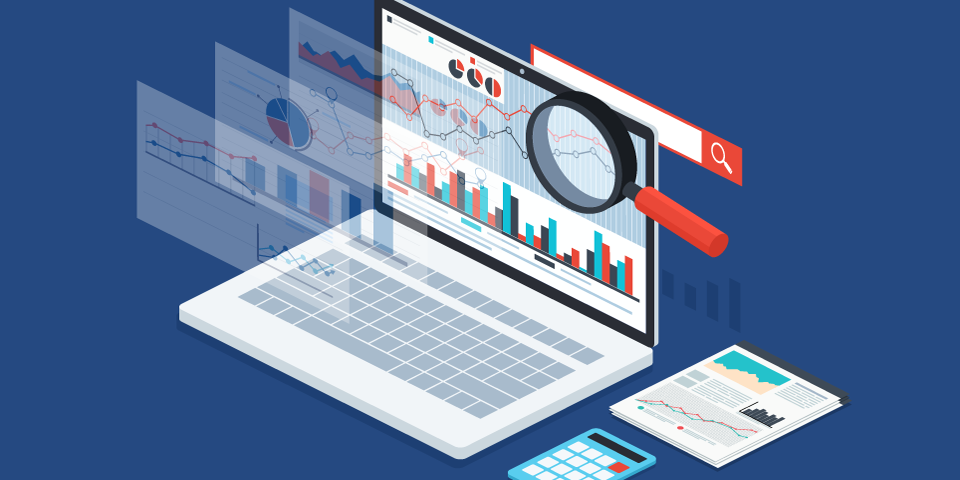
Market Trends, Real Estate Technology
How to Allocate Your CRE Tech Budget in 2025
Discover how CRE leaders are allocating technology budgets in 2025 and beyond.
See Northspyre in action
Get a demo to see how leading developers use Northspyre to work smarter at every stage of the development lifecycle.